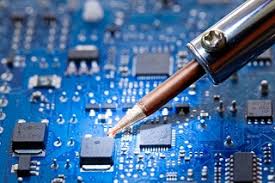
- Enseignant: FEUDJIO Hugues
- Enseignant: Cellule Informatique
Ce cours permet aux étudiants d'acquérir les compétences pour analyser les réseaux électriques linéaires en régimes continu et alternatif.
This course has as main objective to equip students with useful and basic linguistic skills to face the challenges of the university world and to prepare for the TOEIC exam ahead. As a matter-of-fact, this course will help students to read and write notes, scientific pieces of work, books, articles, and to communication easily both at national and international levels. It will also equip them with adequate knowledge to tackle examination papers, given the official bilingual status of ISTAMA/INUBIL.
To this effect, students are urged to regularly attend classes, read their notes, do their assignments and more importantly ask questions during classes to know more about the other official language of our country. It is worth noting that the 100 hours allocated to the course CP I shall be organised between lectures (cours magistral), speaking and listening sessions, videos, tutorials (TD), student’s personal work (TPE), Continuous assessment (CC) and its correction.
Ce cours vise à l' étudiant de comprendre le mécanisme de pilotage des flux au sein d'une unité. nous allons aborder les différentes positions de la supply chain .
Plan du cours
Introduction générale
Chapitre 1 : Les organisations logistiques
Chapitre 2 : Gestion de la flotte matérielle et de la maintenance
Chapitre 3 : Gestion des ressources de production : charge/capacité
Chapitre 4 : Le pilotage et le diagnostic logistique
CHAPITRE 1 : LES OUTILS D’ANALYSE
Il s’agit des outils d’analyse qui peuvent être utilisés pour le diagnostic d’une chaine logistique. Parmi ces outils, on a :
Þ La méthode ABC
Þ Le diagramme d’ISHIKAWA ou diagramme de causes à effet
Þ L’Analyse des Modes de Défaillance, de leurs Effet et leurs (AMDE)
S1- LA METHODE ABC
I- PRESENTATION
Cette méthode permet de classer les composants suivant un critère bien défini. On peut par exemple déterminer les articles ou les composants qui représentent une plus grande part dans l’activité ou le chiffre d’affaire de l’entreprise. Elle consiste à classer ces composants en trois groupes désignés par les lettres A, B et C ; d’où l’appellation méthode ABC. La classe A est celle des composants les plus prépondérants (prioritaires) selon le critère défini ; les éléments de la classe B sont moins prépondérants que ceux de la classe A mais plus prépondérants que ceux de la classe C. En moyenne on observe que la classe A est constitué de 20% de composants qui représentent 80% du critère défini. Ces pourcentages justifient l’appellation 20/80 de cette méthode. Dans la pratique on a :
· La classe A est constituée de 10 à 20% de composants qui représentent 70 à 80% du critère défini.
· La classe B est constituée de 20 à 30% de composants qui représentent 10 à 20% du critère défini.
· La classe C est constituée de 50 à 60% de composants qui représentent 5 à 10% du critère défini.
II- Intérêt et champs d’application
La méthode ABC peut être utilisée dans plusieurs domaines.
ü En gestion des stocks et approvisionnements, elle permet d’adopter une politique de gestion de stock et approvisionnement ; en effet à chaque classe correspondra une méthode de réapprovisionnement.
ü Dans le stockage ou l’entreposage, elle peut permettre d’effectuer un meilleur stockage des composants ou articles avec pour conséquences d’éviter les pertes de temps par un meilleur repérage, de réduire le nombre d’opérations de manutention dans un dépôt ou un entrepôt.
ü Dans une boutique, elle peut permettre un accès aisé aux articles.
ü En maintenance, cette méthode permet par exemple d’identifier les composants qui causent le plus d’arrêts de travail dans une unité de production ou qui contribuent le plus au coût de la maintenance. Dans ce cas on peut alors mettre en place une politique de maintenance permettant de réduire l’influence de tels éléments.
ü Le directeur commercial veut connaître les clients et ce qu'ils représentent par rapport à la totalité de la clientèle. Qui apporte à la société la plus grosse partie du CA ?
ü Le gestionnaire veut connaître les articles en stock qui représentent la plus grosse immobilisation financière.
ü L'acheteur à besoin de connaître les plus gros fournisseurs de l'entreprise et les produits coûteux. etc...
III- La méthodologie
Les étapes pour effectuer le classement sont les suivant :
v Déterminer ou définir le critère d’étude s’il n’est pas donné
v Calculer la contribution en pourcentage (%) de chaque composant selon le critère défini (rapport de la contribution de chaque composant sur la contribution totale) et le pourcentage du nombre de référence pour chaque composant (rapport du nombre de composant par référence sur le nombre total de composants).
v Classer les composants dans un tableau (constitué de lignes et de colonnes) par ordre décroissant de leurs contributions respectives.
v Calculer pour chaque ligne du tableau (chaque composant) :
- Le pourcentage cumulé du nombre de référence
- Le pourcentage cumulé de la contribution
v Déterminer les classes A, B et C en sélectionnant les composants partant du premier dans le tableau suivant les pourcentages liés à ces classes.
On peut ensuite faire une représentation graphique de ce classement en portant les pourcentages du nombre de référence en abscisse et les pourcentages de la contribution en ordonnée.
Remarque 1 :
La méthode ABC est d’autant plus efficace que le nombre de composants est très élevé (au moins 10). Par ailleurs, il peut arriver que les pourcentages obtenus soient légèrement en déca des pourcentages de définitions des classes. Cette méthode peut aussi se solder par une impossibilité de dégager les trois classes ; ce qui peut s’expliquer par le fait que les composants ont relativement la même contribution selon le critère défini.
Remarque 2 : Quelques règles de gestion
Dans le cas de produits destinés à la vente, les règles de gestions suivantes peuvent être appliquées :
o Ruptures de stock non autorisée pour les articles de la classe A ;
o Planification des approvisionnements sur mini/maxi pour la classe A, commandes par lots pour la classe B, et commandes sur besoin pour la classe C ;
o Stock de sécurité accepté pour la classe A, pas de stock de sécurité pour les classes B et C
o Inventaires tournants pour les classes A (tous les trimestres) et B (tous les 6 mois), inventaire annuel pour la classe C.
Exercice1 :
Au cours d’une année, une entreprise a réalisée les approvisionnements présentés dans le tableau suivant :
Référence article |
Quantité |
Coût d’achat unitaire |
A |
300 |
140 |
B |
150 |
4000 |
C |
400 |
2800 |
D |
90 |
250 |
E |
40 |
3200 |
F |
260 |
850 |
G |
140 |
200 |
H |
120 |
580 |
I |
110 |
440 |
J |
250 |
136 |
K |
45 |
2000 |
L |
20 |
1300 |
TAF : classer ces articles selon leurs contributions au coût total d’achat ainsi qu’une représentation graphique.
S2- LE DIAGRAMME D’ISHIKAWA
I-PRESENTATION
Ainsi encore appelé diagramme en arêtes de poisson ou diagramme de cause à effet, le diagramme d’ISHIKAWA est le fruit du japonais KAORU ISHIKAWA concernant la gestion de la qualité. Il est utilisé comme outil de gestion de la qualité et offre la possibilité d’une réflexion en groupe pour la résolution d’un problème. Il peut aussi être utilisé comme outil d’aide au diagnostic. C’est un outil qui récence les causes aboutissant à un effet. Son analyse permet une aide à la décision soit pour corriger un fait existant, soit pour la mise en place d’un projet. Les causes sont reparties en 5 catégories ou familles dont les désignations commencent par la lettre M ; d’où l’appellation méthode des 5M.
Ces familles sont :
· Le milieu : concerne les causes qui sont liées à l’environnement physique et humain. On parle par exemple de l’ambiance du travail, de l’aménagement, le bruit, les odeurs, la propreté, le contact avec le milieu extérieur (les fournisseurs), la législation, le marché…. Le milieu peut être inadapté, sale, mauvais…
· Le matériel : concerne les causes liées à l’équipement, aux machines, les technologies d’outils. Le matériel peut insuffisant, vétuste, inadapté, mal maintenu, indisponible
· Méthodes : concerne les causes liées au mode opératoire ou la façon de faire, à savoir les procédés, les procédures, l’instrumentation, planning, manuels…. Les méthodes peuvent être inexistantes, inadaptés, mal utilisés….
· Main d’œuvre : concerne les causes liées aux ressources humaines directes et indirectes. La main d’œuvre peut être insuffisante, incompétente, âgée, mal formée, non motivée, inadaptée etc…
· Matière : concerne les causes liées aux matières premières et tout ce qui est consommables. La matière peut être de mauvaise qualité, insuffisante, indisponible, couteuse…
le diagramme est composé de flèches comme illustré ci-après. A chaque famille de causes sont rattachées des flèches horizontales portant ces causes. Ces dernieres peuvent à leur tour se voir préciser par des nouvelles flèches obliques portant des sous causes. Le diagramme doit permettre par une arborescence complexe de classer les causes de manière à visualiser l’emboitement. Il devra donc être lisible.
![]() |
|||||
![]() |
|||||
![]() |
|||||
![]() |
|||||
![]() |
|||||
![]() |
II-LE DEROULEMENT
La construction du diagramme passe par les étapes suivantes :
· Définir clairement l’effet sur lequel l’on souhaite agir directement
· Lister les causes les plus probables par un brainstorming (réunion ou les participants donnent leurs points de vue), enquêtes, entretien sur le terrain, questionnaires….
· Regrouper et classer ces causes en familles en se référant aux 5M
· Etablir des sous familles lorsque le nombre de causes par famille le justifie (sous –causes)
· Tracer le diagramme de causes à effet selon l’illustration précédente.
III-ADAPTATION
Dans les trois cas suivant on parlera de diagramme HISHIKAWA adapté
· Dans certains cas d’autres familles peuvent être ajoutées à savoir Management et moyens financiers ; on parle alors de 7M
· Il peut arriver que le regroupement des causes en familles ne permette pas d’obtenir les 5M et se retrouver avec 3M ou 4M par exemple.
· On peut aussi faire un regroupement de causes qui ne ressort pas les M
Exercice d’application :
Dans une unité de production, on a constaté le non respect du niveau de production prévu par le programme directeur des productions (PDP). Les acquêtes menées ont permis de numéroter les causes suivantes :
1. Mauvaise prévision des besoins.
2. Rupture des stocks des matières première des composants.
3. Insuffisance de la matière première.
4. Pane fréquente des machines.
5. Absentéisme du personnel.
6. Mauvaise maintenance des machines.
7. Mauvaise qualité de la matière première.
8. Taux des rebus élevé.
9. Mauvaise qualification de la production.
10. Mauvaise implantation des machines.
11. Espace du travail réduite.
12. Présence des encours
13. Machine vétuste.
14. Procédé de fabrication obsolète.
15. Greve du personnel.
16. Mésentente des employés.
TRAVAIL A FAIRE : Classer ces causes en 5 familles inspirées de 5 M puis tracer le diagramme
S3 : L’AMDE
Historique et présentation
L’analyse des modes de défaillance et de leurs effets (AMDE) est dans l’industrie aéronautique américaine au début des années 1960.
C’est une méthode d’analyse inductive destinée à prévenir les défaillances potentielles d’un produit, d’un système, d’un processus ou d’une organisation. Elle permet de rechercher les causes possibles de ces défaillances. Elle est utilisée comme outil de prévention de la non – qualité.
Les éléments de base
Méthode d’analyse des risques de type dysfonctionnel (non satisfaction des besoins), l’AMDE est basée sur l’établissement de relations de cause à effet. Elle s’appuie sur l’identification des modes de défaillance des composants du système concerné. Pour cela, elle se base sur l’analyse fonctionnelle qui permet de faire une décomposition (analyse structurelle) du système étudié en éléments et en associant à chaque élément sa fonction en la caractérisant. Une description du système concerné par un schéma synoptique ou par un schéma détaillé est aussi nécessaire pour cette analyse.
Le mode de défaillance ou simplement défaillance se définit par rapport à une fonction requise ou attendue. Elle peut être partielle ou totale. Une fonction se définit par un verbe à l’infinitif suivi d’un ou plusieurs compléments.
L’effet se définit par rapport à l’utilisateur du système et est la conséquence de la défaillance pour lui.
La cause est un événement qui entraîne une défaillance donc qui conduit un composant du système à dysfonctionner.
Le déroulement de l’étude AMDE
La demande AMDE se déroule typiquement en 5 étapes :
N°1 : l’Initialisation : cette étape vise à définir le périmètre de l’étude (sujet, objectif, limites de l’étude,…)
N°2 : la préparation : il s’agit de collecter l’ensemble des données d’entrée de l’étude (analyse fonctionnelle, description des solutions, méthodes et processus de production).
N°3 : l’Identification des modes de défaillance : on analyse, pour chaque fonction attendue, les modes de défaillance des composants ou constituants qui conduisent au non – respect des caractéristiques attendues. Pour chaque mode de défaillance, on déclinera l’effet (impact sur le client), la cause (quel phénomène est l’origine de la défaillance) ainsi que la détection (quels sont les moyens de contrôle existant et leur efficacité).
A l’issue de cette étape, on élabore un tableau illustré ci – après :
Composant |
Fonction |
Défaillance |
Effet |
Cause |
Contrôle |
|
|
|
|
|
|
N°4 : Recherche d’actions préventives : il s’agit de recenser les actions destinées à prévenir les modes de défaillances.
N°5 : Mise en œuvre des solutions : Une fois identifiées les actions à mettre en œuvre pour augmenter, il faut les appliquer. Il faudra ensuite procéder au suivi de l’efficacité de ces actions.
EXEMPLES :
AMDE d’un système logistique classique d’une entreprise à but lucratif constitué des 3 maillons classiques : Approvisionnement, Production ou Transformation et Distribution
Composant |
Fonction |
Défaillances |
Causes |
Effets |
Moyens de détection |
APPROVISIONNEMENT
|
Mettre à la disposition de la production les matières premières et composants (MPC)
|
1.Pas de mise à disposition des MPC (Rupture de stock des MPC) 2.Insuffisance des MPC 3.Mauvaise qualité des MPC |
.Retards de livraison par les fournisseurs .Mauvaise GSA des MPC .Indisponibilité du personnel .Mauvaises informations en provenance de PRODUCTION |
Mécontentement des clients Baisse du Chiffre d’Affaires |
.Visuel .Contrôle de qualité
|
PRODUCTION |
Transformer les MPC en produits finis (PF) |
4.Pas de transformation des MPC (Arrêt de la production) 5.Insuffisance des PF 6.Mauvaise qualité des PF
|
1, 2, 3. .Mauvaise planification de la production .pannes des équipements .Indisponibilité du personnel .Mauvaises informations provenant de DISTRIBUTION |
.Visuel .Contrôle de la qualité |
|
DISTRIBUTION |
Mettre à la disposition des clients les PF |
7. Pas de mise à disposition des PF aux clients (Rupture de stock des PF) 8.Mauvaise qualité de service |
4, 5, 6. . Mauvaise GSA des PF .Indisponibilité des véhicules .Indisponibilité du personnel
|
. Visuel . Plaintes des clients |
S4 : METHODE DES 5 S
Sommaire
Définition de la méthode 5S
La méthode 5S permet d'optimiser en permanence les conditions de travail et le temps de travail en assurant l'organisation, la propreté et la sécurité d'un plan de travail.
La méthode 5S est d'origine japonaise. Elle a été créée pour la production des usines Toyota. La méthode 5S est une technique de management qui fait partie de la démarche qualité.
Les 5S proviennent des cinq opérations qui constituent la méthode :
Mot japonais |
Actions associées |
Seiri |
Trier, jeter, recycler, archiver, placer les outils de travail selon leur fréquence d'utilisation. |
Seiton |
Ranger, classer de manière à limiter les déplacements physiques ou le port d'objets lourds, optimiser l'utilisation de l'espace. |
Seiso |
Nettoyer, réparer. |
Seiketsu |
Ordonner les documents ou son poste de travail de manière à ce qu'une autre personne puisse s'y retrouver. |
Shitsuke |
Être rigoureux, appliquer les 4 opérations précédentes et les maintenir dans le temps. |
Les 5S ont été inventés pour les ateliers, mais ils s'appliquent aussi bien dans les services et les bureaux.
Les avantages des 5S sont nombreux :
Application de la méthode 5S
Appliquer la méthode 5S est bénéfique pour l'entreprise. La méthode 5S peut être utilisée par les petites, moyennes et grandes entreprises.
Gestion de la méthode 5S
Mise en place de la méthode 5S
La méthode 5S est le plus souvent mise en place par :
Dans un premier temps, la mise en place de la méthode 5S passe par la création d'affichage et de planning organisant les actions à mener.
Ensuite, les responsables de service ont à leur charge l'application, le respect et le maintient des actions de la méthode 5S.
Réussite de la méthode 5S
Si la méthode 5S est une réussite, l'entreprise est plus performante. Les employés sont plus heureux et la productivité est augmentée.
Pour que cette réussite soit durable, l'entreprise doit en permanence s'assurer que les règles mises en place dans le cadre de la méthode 5S soient respectées, mais aussi récompenser ses employés en cas de bons résultats.
Méthode 5S : Gagnez en efficacité en améliorant votre environnement de travail
Vos collaborateurs
mettent 5 minutes à retrouver un document sur leur bureau, ou encore un outil
dans leur espace de travail ? Voir un tel environnement
encombré et surchargé ne les motive plus à travailler, ou à s’impliquer pour
atteindre l’objectif ?
Optez pour la méthode 5S qui résoudra tous ces problèmes d’organisation au sein de vos services,
bureaux, ateliers.
Définition de la technique de management les 5S
La méthode 5S est une pratique d’optimisation des conditions et de l’environnement de travail, du temps de travail en veillant à ce que cet environnement reste bien rangé, nettoyé, sécurisé, en y instaurant de la rigueur. Le 5S est un système de travail facile et rapide à mettre en place. D’origine japonaise, elle est constituée de 5 étapes. Plusieurs significations peuvent être associées. Tout dépend de votre activité car les 5S ont été conçus pour les ateliers, les usines mais peuvent très bien s’adapter dans les services, les bureaux ou encore chez vous ! Voici en détails les 5S de la méthode 5S du Lean Management.
ELIMINER, c’est la première des priorités des 5S. Commencer par se débarrasser de tout ce dont on n’a pas besoin. Il est important de garder mais aujourd’hui il est tout aussi important de jeter. Et surtout ce qui est fondamental, c’est de savoir ce qui doit être gardé ou jeté.
RANGER, c’est placer quelque chose à un endroit précis afin de pouvoir le retrouver tout de suite dès qu’on en a besoin et ainsi éviter de perdre du temps à chercher.
NETTOYER, le nettoyage des bureaux, des lieux de travail et des moyens de production va bien au-delà de la propreté. En ce qui concerne les machines et l’outillage par exemple, c’est un premier pas vers l’auto-maintenance : souvent, c’est au moment du nettoyage que l’on détecte les anomalies et les usures prématurées.
STANDARDISER, c’est à ce stade que sont définies les règles par lesquelles le lieu de travail restera débarrassé des objets inutiles, rangé, nettoyé. Pour éliminer les risques de désordre, Takashi Osada préconise le management visuel qui s’appuie sur un certain nombre d’aides.
RESPECTER, il faut respecter les règles précédemment établies et donc encourager le personnel à adhérer à ces règles. Il s’agit de faire systématiquement ce qu’il faut faire, de faire en sorte que les 5S deviennent une habitude.
Démarche créée par le TPS, Toyota Production System
La méthode 5S a été développée par le groupe Toyota dans le cadre du TPS, Toyota Production System. La démarche 5S a pour but d'améliorer l’environnement de travail du collaborateur, mais ce n'est pas la seule méthode Lean créée par Toyota. Inspiré du Fordisme, le Toyotisme s’est avéré efficace et a été approfondi afin de créer les 5S. Cette technique remodelée a fait ses preuves à travers le temps. C’est un outil de gestion d’entreprise permettant :
But de la technique de management : les 5S
Le progrès est possible si tous s’engagent ensemble. Cet engagement collectif commence par la prise en compte de l’environnement de travail de chacun (machine, ligne, laboratoire, bureau, magasin…).
Au-delà d’une simple technique d’ordre, les 5S sont surtout une méthode de management participatif permettant de responsabiliser le personnel dans l’amélioration de l'organisation d’un site. Cette action nécessite la participation de tous les niveaux hiérarchiques.
Les 5S sont un
prérequis indispensable dans la démarche d’amélioration continue : ils permettent de partager l’état d’esprit
nécessaire à l’amélioration continue.
La méthode 5S se base sur la constatation qu’un espace propre et bien rangé est
propice à une production de bonne qualité.
Avantages de la méthode 5S, résultats directs
Avantages de la méthode 5S en termes de comportements
Des exemples de l'utilisation du 5S
Poste de travail avec les 5S
La méthode 5S valorise l’image de vos postes de travail, établis, îlots, secteurs, ateliers de production et offre :
Bureau avec les 5S
Cette technique de management offre une solution complète au sein de l’entreprise, des services, des bureaux tels que :
La signalétique par les 5S
Cette démarche pour un environnement propre, organisé et fonctionnel propose d’utiliser la signalétique afin de permettre :
Comment réussir à mettre en place sa méthode 5s ?
L’approche 5S est
participative. En production, les opérateurs sont sollicités pour repenser le
travail de manière efficiente, en fonction de leur expérience, des contraintes
au quotidien et des idées d’amélioration qu’ils vont proposer et mettre en
œuvre. Ce mode de déploiement est particulièrement motivant. Les participants
s’impliquent fortement.
La mise en place des 5S est également l’opportunité d’enrichir
les tâches des opérateurs, notamment en leur déléguant l’entretien courant des machines et des équipements. Une formation dispensée par les experts de la
maintenance peut s’avérer nécessaire. Pour une bonne partie des opérateurs
concernés, cet enrichissement des tâches est vécu très positivement. Il
valorise leur poste au-delà de la simple conduite de machine et les implique au
quotidien.
CHAPITRE 2 : DISTRIBUTION PHYSIQUE
Introduction générale
La distribution physique constitue le maillon aval de la chaîne logistique classique qui comprend en amont l’approvisionnement et au milieu la production.
C’est l’ensemble des activités ou opérations qui permettent de mettre les produits fabriqués à la disposition des clients. Elle recouvre toutes les activités ou opérations situées en aval de la production telles que :
v Le stockage ou entreposage
v Le traitement des commandes
v La préparation des expéditions
v La manutention
v La livraison (transport terminal).
Son objectif est d’assurer, à moindre coût, un niveau de service de plus en plus élevé avec des délais de plus en plus courts. Elle constitue alors un secteur où les entreprises peuvent faire la différence.
La recherche de la performance dans ce domaine conduit à la rationalisation de l’organisation des flux internes de l’entreprise :
Þ Sur le plan opérationnel, il faut définir les systèmes de gestion de stock et approvisionnements, les méthodes de travail dans les dépôts et entrepôts ainsi que l’organisation des tournées de livraison.
Þ Sur le plan structurel, il faut définir les structures des réseaux de distribution ce qui consiste à définir le nombre d’étages (dépôts et/ou entrepôt), leurs localisations, leur capacités ainsi que leur degré d’automatisation et d’informatisation.
Cette partie sera subdivisée en trois chapitres à savoir/
v Les réseaux de distributions
v L’affectation « usines – dépôts »
v L’organisation des tournées de livraison
S1 : LES RESEAUX DE DISTRIBUTION
Dans ce chapitre, il s’agit de décrire les différentes structures possibles des réseaux de distribution, d’examiner le problème de la localisation d’un dépôt ou d’entrepôt ainsi que celui du choix du nombre de dépôts.
A/ Les différentes structures
On distingue globalement la structure directe (sans étage) et la structure indirecte (avec étages). Elles sont décrites ci – après.
a)La structure sans étage
Il s’agit de la distribution directe. Les clients sont livrés à partir du stock de l’usine ou des usines d’où sont effectuées les opérations de traitement des commandes et de préparation des expéditions. Elle se schématise comme suit :
Flux de produits finis
Exemple d’entreprise pratiquant ce type de réseau : SOCAVER, SABC, CIMENCAM, GUINNESS car fait plus intervenir les grossistes. Structure utilisée lorsque les quantités à livrer sont trop importante.
b)La structure à un étage avec un entrepôt central
Dans ce cas l’entrepôt reçoit les productions des usines, gère un stock, traite les commandes, prépare les expéditions et réalise ou fait réaliser les transports terminaux (livraisons) vers les clients. Elle se schématise comme suit :
1) La structure à un étage avec un ensemble de dépôts locaux
Chacun de ces dépôts joue le même rôle que l’entrepôt central dans le cas précédent pour la région qu’il dessert. Elle se schématise comme suit :
Les dépôts reçoivent les productions des usines et dans ce cas le problème de l’affectation des productions des usines aux différents dépôts peut se poser. Il sera abordé au prochain chapitre.
2) La structure à deux étages
Dans ce cas il y a deux niveaux entre les usines et les clients ; ces niveaux peuvent être constitués de :
Þ Un entrepôt central et un ensemble de dépôts locaux
Les
usines approvisionnent l’entrepôt central qui ravitaille les dépôts locaux. Ces
dépôts conservent des stocks, traitent les commandes et livrent aux clients.
Elle ss schématise comme suit :
![]() |
|||||
![]() |
|||||
![]() |
|||||
Þ Un entrepôt central et un ensemble de plates – formes de distribution ou d’éclatement
La préparation des commandes de clients s’effectue directement dans l’entrepôt central qui reçoit les productions des usines et gère un stock. Les produits sont ensuite acheminés jusqu’à des plates – formes régionales où après déchargement (sur un quai par exemple) puis rechargement dans des « petits véhicules » parviennent aux clients par des tournées de livraison. Ces plates – formes ne disposent pas de stocks de produits. Cette structure se schématise comme suit :
Légende :
Plate - forme
Point de
livraison
Tournée de livraison
Flux de produits finis
La structure à deux étages concerne surtout la distribution à l’international qui implique les sociétés qui délocalisent leurs usines de production vers les pays où la main d’œuvre est bon marché, ensuite regroupe les différents produits dans un pays où se trouve le siège social pour après organiser la distribution vers d’autres pays.
Remarque : selon sa typologie et la nature de sa clientèle, une entreprise peut combiner structure directe et structure indirecte.
B/Localisation d’un dépôt ou d’un entrepôt
1) Problématique
Dans une structure à étage (s), l’une des questions qui se posent est celle de savoir où implanter un entrepôt ou un dépôt. Il faut donc déterminer le meilleur emplacement pour cette implantation ; les critères selon lesquels cet emplacement est meilleur sont variés et relatifs. Ainsi, ce choix peut se faire en cherchant à diminuer :
- Les coûts de transport qui sont plus ou moins proportionnels à la distance seule ou à la distance et au tonnage transporté
- La durée de transport qui dépend des distances et du réseau routier urbain voire interurbain
Une approche réaliste serait de considérer la durée de transport comme simple contrainte dans l’objectif de minimiser les coûts de transport et le problème serait formulé comme suit : « choisir le meilleur emplacement pour minimiser les coûts de transport en respectant un délai ou des délais en temps ».
Si l’on prend en compte le contexte des échanges internationaux, ce choix peut être influencé par la disponibilité des entrepôts dans les ports et aéroports.
Plusieurs méthodes permettent d’obtenir des solutions qui constituent davantage des outils d’aide à la décision que des solutions optimales.
2) Recherche d’une solution
Parmi les méthodes qui peuvent aider à trouver une solution, on a la méthode du barycentre et la méthode de centration.
2- 1 la recherche barycentrique
Cette méthode consiste à formaliser l’origine et les destinations des flux globaux de l’entreprise dans une même unité en terme de poids et de distance puis à relier deux à deux des destinations entre elles et ainsi de suite. Entre les poids moyens définis jusqu’à les relier entre eux. Le point d’équilibre désigne l’endroit où l’on va situer l’entreposage. Ce point est représenté par des coordonnées longitudinales et sur le plan latéral.
E : longitude (x),
latitude |
E(x,y) avec
|
|
|
et
|
|
CAS D’APPLICATION : L’entreprise LSC S.A installée en Italie depuis plus de 30 ans voudrait implanter une représentation au Cameroun spécialisée dans la production et la distribution des pâtes alimentaires. Le chef de ce projet vous retient comme stagiaire et conditionne votre recrutement sur la qualité de la prestation que vous allez fournir dans le processus d’installation de l’entrepôt central. Il vous confie à cet effet des données suivantes :
Villes à livrer Distance (longitude x) Distance (latitude y) Poids de la marchandise (g)
Douala 26 14 42.000
Yaoundé 28 16 24.000
Bafang 20 23 15.000
Limbé 27 25 30.000
Maroua 20 30 10.000
Ebolowa 25 18 12.000
Total
Travail à faire : Déterminer le point idéal pour la localisation du futur entrepôt par la méthode barycentrique.
Les principaux problèmes que pose cette méthode sont :
Elle induit que les coûts de transports sont linéaires
Les frontières entre barycentre n’en sont pas finement prises en compte
|
Les notions de temps de livraison liés aux tracasseries policières, à la qualité des infrastructures routières et à la qualité des moyens de transport sont généralement négligées |
Cependant l’intérêt de cette méthode est qu’on peut l’appliquer sur toute notion d’espace.
2 - 2 Méthode centrique ou de centration
L’exemple précédent nous indique que le magasin peut être implanté dans la région d’Ebolowa. Mais cette méthode n’indique généralement pas avec précisément le point idéal c’est pourquoi il faut la compléter avec la méthode centrique. La méthode centrique s’inscrit sur la même logique mais prend en compte le nombre de voyage.
Exemple d’application Cas LSC S.A (Suite)
Vous expliquez à votre directeur de stage que la méthode barycentrique ne vous permet pas de décider avec précision et exiger de lui des informations pour que vous puissiez appliquer la méthode de centration. Il vous confie à cet effet des informations sur les villes de Douala, Yaoundé, Bafang et Ebolowa suivi de la carte d’implantation et du programme de livraison pour le mois de Février.
Point |
Douala(A) |
Yaoundé(B) |
Bafang(C) |
Ebolowa(D) |
Douala(A) |
|
250 km |
500 km |
600 km |
Yaoundé(B) |
|
|
9400 km |
8250 km |
Bafang (C) |
|
|
|
4200 km |
Ebolowa (D) |
|
|
|
|
Sachant que le kilométrage d’une ville est égal au nombre de voyage multiplié par la distance qui sépare cette ville des autres villes.
Déterminer le lieu idéal d’implantation du futur entrepôt sachant que le programme prévoit que pour le mois de Février les commandes par ville étaient reparties de la façon suivante: Douala 10; Yaoundé 6; Bafang 14; Ebolowa 8.
Introduction générale
Un système logistique est un ensemble de méthodes et de technologies que met en place une entreprise afin de gérer et d’organiser le flux de ses produits.
Un système logistique permet donc de : Préparer, Trier, Conditionner, Stocker, Palettiser, Entreposer, des produits dans le but de les mettre à disposition selon les besoins de l’entreprise.
Le système logistique concerne les activités de la logistique amont et de la logistique aval.
Dans la logistique amont on peut citer :
- Le management des matières (planification et contrôle des flux de matières premières).
- Les approvisionnements
- L’entreposage
- La production
- Le transport amont
- La réception, le contrôle qualité des matières et la gestion des stocks des matières premières.
Dans la logistique aval ou distribution physique ;
Elle concerne le service clients et les opérations de la chaine de distribution.
Elle partage la plupart des activités ou processus de la logistique amont.
La retro logistique ou reverse logistique de retour.
La logistique est l’ensemble des opérations ou méthodes qui consiste à produire et acheminer les biens ou les services au bon moment et au bon endroit et dans les meilleures conditions de qualité, de coût, de délai et de sécurité. Elle peut aussi être définie comme l’organisation matérielle des activités d’une entreprise. Elle coordonne toutes les activités liées à la circulation des marchandises intervenant dans les domaines comme l’approvisionnement, la production, la manutention, le conditionnement, l’emballage, l’entreposage, le transport, la distribution jusqu’au point de vente.
Face au grand défi de se maintenir toujours à un haut niveau de compétitivité, les entreprises mettent l’accent sur les performances techniques, sur les innovations gestionnaires, sur le niveau de service à la clientèle. Pourtant, la grande majorité des entreprises est confrontée aux contraintes de marché tel que :
- Les exigences de la clientèle
- La qualité du produit ou service
- La réduction des délais et des coûts
- La diversification (manufacturation de plusieurs produits ou prestation de plusieurs services)
- La fiabilité des marchés
- Les coûts de transport
- La réduction des stocks
- Les coûts administratifs
- La concurrence
- …
Se sont les domaines à améliorer pour atteindre la performance globale en entreprise. Pour répondre à cette exigence l’on doit fixer des objectifs dans chacun de ces domaines, les associés pour définir la véritable performance logistique en cohérence avec la performance globale de l’entreprise.
CHAPITRE 1 : LES ORGANISATIONS LOGISTIQUES
Section 1 : la distribution physique
La
distribution physique est l’ensemble des activités qui
permettent de mettre à la disposition des clients les produits
finis. Parmi
ces activités on peut citer : L’entreposage ; le traitement des commandes ; la
préparation des expéditions ; la manutention ; la
livraison ou le transport
Son objectif
est réduire les coûts, améliorer la qualité du service et respecter les délais.
La distribution physique a pour but de mettre à la disposition du client les produits fabriqués. Elle recouvre toutes les activités ou opérations situées en aval de la production à savoir le stockage, le traitement de commandes, préparation des expéditions, la manutention et la livraison au client (transport). L’un des objectifs de cette fonction est d’assurer au moindre coût un niveau de service de plus en plus élevé et les délais sont de plus en plus courts.
Elle constitue alors un secteur dans lequel les entreprises peuvent faire la différence. La recherche d’une meilleure performance dans ce domaine conduit à l’optimisation de l’organisation des flux internes de l’entreprise :
Ø Sur le plan opérationnel : il faut définir le système de gestion des stocks et de réapprovisionnement des procédures de travail dans les dépôts, l’organisation des tournées de livraison ;
Ø Sur le plan structurel : il faut définir les structures de réseaux de distribution et en particulier le nombre d’étages (l’entrepôt central, dépôt) leur localisation et leur capacité ainsi que leur degré d’automatisation et d’informatisation ;
La distribution engendre des coûts, on peut citer ;
a)-Le coût d’entreposage.
- L’entretien et les moyens de stockage.
- Le personnel d’encadrement (formation),
- Le coût d’exploitation ou de fonctionnement de l’entrepôt.
- Les taxes et impôts.
b)-Le contrôle de réception.
- Le personnel de manutention.
- Les moyens de manutention
- La préparation des commandes
- Les transports avec sans ou rupture de charge.
- Les moyens propres ou partagés
- Le taux de remplissage des moyens de transport
- La distance
- Le traitement des informations.
Ce chapitre se subdivise en 03 sections : les réseaux de distribution, l’affectation usine dépôt, l’organisation des tournées de livraison.
A. STRUCTURE DE DISTRIBUTION
Il s’agit de décrire les différentes structures possibles et examiner le problème de la localisation d’un entrepôt ou d’un dépôt et du choix du nombre de dépôts.
La structure de distribution définit les réseaux utilisés par le produit pour parvenir au consommateur final. La structure peut être directe ou indirecte.
1) DIVERSES STRUCTURES DES RESEAUX DE DISTRIBUTION
On peut en citer quatre :
Ø Structure sans étage ou directe : il s’agit de la livraison directe, les clients sont livrés à partir des stocks de(s) usine(s) sans dépôt ou entrepôt intermédiaire. Elle se schématise comme suit :
Cette option est utilisée lorsque les quantités à livrer sont très importantes.
Ø Structure à un (01) étage avec entrepôt central : dans ce cas l’entrepôt reçoit les produits des usines, gère un stock, prépare les commandes et (réalise ou fait réaliser les transports terminaux vers les clients). Cette structure se schématise ainsi qu’il suit.
Ø Structure à un(01) étage avec plusieurs dépôts locaux : chacun de ces dépôts joue un rôle que l’entrepôt central dans le cas précédent pour la région qu’ils desservent. Les dépôts reçoivent les produits des usines et dans ce cas le problème de l’affectation des produits des usines aux clients se pose. Cette situation se schématise ainsi qu’il suit :
Ø Structure à deux(02) étages : dans ce cas il ya 02 niveaux entre les usines et les clients qui peuvent être constitués de :
· Un entrepôt central et un ensemble de dépôts locaux. Les usines approvisionnent l’entrepôt central qui fournit les dépôts locaux et ces derniers conservent les stocks et les livre aux clients. Dans ce cas on a le schéma suivant :
· Un entrepôt central et un ensemble de plate forme de distribution ou d’éclatement. Dans ce cas la préparation de commandes des clients commence à l’entrepôt central.les produits sont acheminés jusqu'à des plates formes régionales ou après déchargement sur le quai puis rechargement dans de petits véhicules, ils parviennent au client par des tournées de livraison. Cette structure se schématise ainsi qu’il suit :
![]() |
,
,
= plate forme
c)- Les facteurs à prendre en compte pour la conception d’un réseau de distribution.
La disponibilité des produits imposés par les clients (délai entre la commande et la livraison).
· Les flux physiques à traiter.
- Les quantités moyennes de produits
- Les variétés.
- La variabilité et la saisonnalité de la demande.
- Les caractéristiques physiques et chimiques des produits
- Le coût global de la distribution.
3)-Les avantages et inconvénients des types de réseaux de distribution.
a)-réseaux à deux étages (entrepôt central et réseaux de dépôts locaux).
Avantages :
- Transport d’approche simple
- Livraison terminale simple
- Proximité des clients
- Délai court.
Inconvénients.
- Stocks élevés
- Opérations de manutention élevées.
b)-Réseau avec plusieurs dépôts locaux.
Avantages :
- Proximité des clients
- Livraison terminal simple
- Délai court.
Inconvénients :
- Stocks élevés
- Transport d’approche complexe
- Beaucoup de manutention.
c)-Système avec un entrepôt central.
Avantages ;
- Transport d’approche simple
- Moins de stocks
- Centration des opérations
- Mutualisation des ressources
Inconvénients.
- Délai
- Livraison terminale complexe
- Loin des clients.
d)- Réseau direct système avec livraison directe
Avantages :
- Flux d’information rapide
- Moins de stocks
Inconvénients ;
- Loin des clients
- Délai de livraison long
- Livraison terminale complexe.
Entrepôt central avec plateforme d’éclatement.
Avantages ;
- Absence de stocks.
Inconvénients ;
- Manutention élevée avec rupture de charge.
3.)-Arbitrage des systèmes ou réseaux de distribution.
On peut disposer localement du stock de tous les produits susceptibles d’être demandés. (Cas de la livraison directe).
Soit effectuer les livraisons dans un délai compatible avec les besoins des clients, d’où la multiplication des transports.
4)-Solutions intermédiaires.
Lorsqu’il y a éloignement des clients dans les différentes zones géographiques, alors les réseaux indirects ou avec étages sont nécessaires pour se rapprocher des clients.
On peut aussi choisir de conserver localement à l’usine les articles les moins vendus (classe B et C) et conserver les articles les plus vendus dans un entrepôt central (classe A).
5)- LOCALISATION D’UN ENTREPOT OU D’UN DEPOT
a-Problématique
On veut chercher à déterminer le meilleur emplacement pour un entrepôt, pour un dépôt. Les critères selon lesquels ces emplacements est le meilleur sont variés et relatifs, ainsi ce choix peut se faire en cherchant à diminuer :
Ø les coûts de transport qui sont plus ou moins proportionnels à la distance seule ou à la distance et au tonnage transporte ;
Ø les durées de transport qui dépendent des distances et du réseau routier urbain voire interurbain ;
Une approche plus réaliste serait de considérer la durée de transport comme simple contrainte dans l’objectif diminuer les coûts de transport et le problème serait formule ainsi qu’il suit «choisir un meilleur emplacement pour minimiser les coûts de transport en respectant un délai ou des délais à temps». Si l’on prend en compte le contexte des échanges internationaux, ce choix peut être influence par la disponibilité des entrepôts dans les ports et les aéroports. Plusieurs modélisations mathématiques et approches permettent d’obtenir des solutions qui constituent davantage des outils d’aide à la décision que des solutions optimales.
b-Recherche d’une solution pour l’implantation d’un entrepôt ou d’un entrepôt
Parmi les méthodes qui peuvent aider à trouver une solution nous avons la méthode du barycentre et la méthode de centration.
Exercice d’application : On considère quatre (04) points A, B, C et D tels que la distance d(AB) = 200 km, d(AD) = 150 km, d(AC) = 100 km, d(BC)= 300 km, d(BD) = 90 km, d(CD) = 150 km
TAF :
1- Trouver le meilleur emplacement du dépôt si celui-ci doit coïncider avec un de ses 04 points (considérant que les flux sont les mêmes)
SECTION 2 : LIVRAISON
Pour une entreprise qui dispose de plusieurs clients à livrer dans les délais précis, celle-ci doit pouvoir organiser les tournées de livraison par la détermination du nombre et la composition des tournées optimal en respectant les contraintes (délais, capacité camion, nature produit...)
1) Les types de tournées
Ø Les tournées fixes : le circuit est établi une fois pour toute. Cette stratégie favorise la
Simplification du travail d’organisation mais le taux de remplissage est faible et cause une
Rigidité du parcours
Ø Les tournées semi variables : les secteurs géographiques sont fixes mais les tournées sont élaborées en fonction des commandes reçues et du cumul des tonnages. Cette méthode optimise le remplissage du camion
Ø Les tournées variables : les tournées sont réactualisées chaque jour d’après les commandes recueillies. Il y a optimisation des ressources matérielles et humaines mais le travail d’organisation demeure complexe.
SYNTHESE
Types de tournées |
Principes de planification |
Avantages |
Inconvénients |
Les tournées fixes |
La composition des circuits reste inchangée, quant aux périodes et points à desservir. |
Simplification de la mise en œuvre. |
-Ne garantit pas un remplissage optimal des véhicules -N’optimise pas l’organisation des tournées en terme de clients à livrer et de distance minimum à parcourir |
Les tournées variables |
Les tournées sont fixées chaque jour, en fonction de la demande et des véhicules disponibles |
Il y a optimisation des ressources matérielles et humaines. |
La mise en œuvre est complexe et laborieuse, vue le nombre variable de véhicules engagés |
2) Préalable à l’organisation des tournées
L’organisation de la tournée est une démarche qui passe globalement par deux étapes fondamentales : La collecte des informations nécessaires puis la détermination des différents circuits de desserte ainsi que leur composition. Les cinq 1ères tâches successives à exécuter dans la mise en œuvre de la 1ère étape (recueillir un certain nombre d’informations) sont :
Le nombre de véhicules et leurs capacités
La localisation des clients
La distance entre les clients, la distance entre les clients et les dépôts
La nature et la quantité des marchandises à transporter
Les délais
Les temps de parcours entre les points et les temps de chargement aux différents points
3) Organisation des tournées de livraison
La fonction objective est : La minimisation des distances parcourues, compte tenu du respect des contraintes relatives aux points à desservir. Elle consiste à déterminer le nombre et la composition des tournées. Cette tâche peut être faite par intuition ou par expérience. Mais les méthodes scientifiques peuvent aussi être utilisées pour résoudre ce problème notamment la méthode des écartements : Algorithme de Kruskal
Mise en œuvre de l’algorithme de Kruskal
L’algorithme de KRUSKAL se déroule de la manière suivante :
Recueillir les informations sur la distance des clients
Calculer les écartements de tous les points à desservir
1)Détermination du nombre d’écart à calculer :
n = nombre de clients à desservir
1) Calculer les écartement entre les couples
2) On classe le couple par ordre décroissant
3) On effectu la tournée San contrainte
4) On effectu la tournée avec contrainte
1- Définition
|
℮ (A, B) représente le gain obtenu en intégrant les 02 points dans une même tournée.
Le principe de l’algorithme repose sur le fait que minimiser la distance totale revient à maximiser la somme des écartements des couples de points.
4) Affectation usine dépôt : la méthode de Stepping Stone
C’est une méthode utilisée pour résoudre certains problèmes de programmation linéaire tels que les affectations usine-dépôt c’est-à-dire partant des différentes usines, il faut satisfaire les différents entrepôts ou dépôts compte tenu de leur capacité respective. La solution à ce problème est donnée en deux étapes :
Ø On va d’abord déterminer une solution de base non optimale qui sera par la suite améliorée. Cette solution de base est obtenue à partir du principe de HOUTHAKKER (de préférence) et/ou le principe Coin Nord-ouest.
- Le principe HOUTHAKKER
Le principe consiste à commencer l’affectation des quantités par la case qui a le coût unitaire de transport le plus petit ou le bas possible à un dépôt ou entrepôt qui peut être satisfaite entièrement tout en respectant les contraintes d’offre et demande ensuite on cherche l’usine qui le coût unitaire de transport le plus petit non saturé et on affecte. Autrement dit Il consiste à desservir les dépôts par ordre croissant des coûts unitaires de transport en respectant les contraintes (on dessert d’abord les circuits aux coûts moins élevés).
- Le principe Coin Nord-Ouest
Le principe de la méthode consiste à remplir au maximum la case en haut et à gauche (Coin Nord-Ouest) puis compléter la ligne ou la colonne de façon à atteindre l’offre ou la demande, continuer ainsi en complétant les cases immédiatement à droites ou en dessous alternativement.
Ø On va procéder à des améliorations (itération), en transférant des unités des circuits aux coûts de transport plus élevés vers des circuits aux coûts de transport moins élevés. Les transferts se font au moins entre 4 points afin de respecter les contraintes. Un transfert créé une valeur ajoutée lorsque son résultat est négatif. Les cases donatrices auront leur coût unitaire transport négatif et les cases réceptrices auront leur coût unitaire de transport positif.
NB 1 : une case ne peut donner à une autre que lorsqu’elle a une quantité
NB 2 : pour trouver la quantité déplacer on va se servir des deux cases donatrice (celles qui portent le signe moins) et on choisit la plus petite quantité entre les deux dans le cas où les quantités sont différentes.
De manière générale le tableau se présente comme suit :
|
|
D1 |
D2 |
…….. |
Dn |
Capacité des usines (offre) |
|
U1 |
|
|
|
|
|
|
U2 |
|
|
|
|
|
|
U3 |
|
|
|
|
|
Demande des dépôts |
|
|
|
|
|
|
Xij c’est la quantité de matière que l’usine i enverra au dépôt j
Exercice 1
Le gérant d’un système de distribution reliant trois usines U1, U2, U3 et quatre grossistes désignés par G1, G2, G3 et G4 souhaite minimiser les coûts de transports pour cette distribution. Les capacités de production de ces trois usines sont respectivement de : 400 unités pour U1, 1500 unités pour U2 et 900 unités pour U3. Les demandes des grossistes sont de 700 unités pour G1, 600 unités pour G2, 1000 unités pour G3 et 500 unités pour G4.
Les coûts de transport (en FCFA par unité transportée), sur chacune des liaison « usine-grossiste » sont regroupés dans le tableau suivant :
|
G1 |
G2 |
G3 |
G4 |
U1 |
20 |
40 |
70 |
50 |
U2 |
100 |
60 |
90 |
80 |
U3 |
10 |
110 |
30 |
200 |
TAF :
1) faire une mise en équation du problème par la méthode de programmation linéaire
2) déterminer l’affectation « optimal » par la méthode Stepping-stone et évaluer son coût.
CHAPITRE 2 : GESTION DE LA FLOTTE MATERIELLE ET DE LA MAINTENANCE
A. Gestion d’un parc automobile
§ C’est une activité qui se pratique pour tous les modes de transports. En transport maritime (gestion de la flotte des navires) ; en transport aérien (gestion de la flotte des aéronefs) ; en transport ferroviaire (gestion des voitures pour passagers, des wagons pour marchandise, des UTI-Unité de Transport Intermodal…) ; en transport routier (gestion des véhicules pour le transport de personnes et véhicules pour le transport de marchandises).
§ La gestion de parc automobile se pratique dans les services « Production ou exploitation » des compagnies de transport et de location de voitures, dans les services « généraux » ou « logistiques » des entreprises industrielles ou commerciales. Les services généraux gèrent le parc de véhicules affectés au transport du personnel de l’entreprise (véhicules utilitaires). Dans les services logistiques, on gère essentiellement le parc de véhicules destinés au transport des marchandises et les engins de manutention. Dans tous les cas, le parc de véhicules géré peut être interne ou externe à l’entreprise.
§ Quel que soit le type d’entreprise ou le mode de transport, la gestion du parc automobile intègre les mêmes activités et responsabilités. Son but est d’optimiser les coûts logistiques, de planifier l’emploi des véhicules de transport et engins de manutention, de garantir la disponibilité de ces derniers pour d’éventuels besoins logistiques ou de transport (mise en œuvre des contrôles techniques, mise à jour des documents de bord, suivi des chauffeurs, gestion des stocks de carburant et des pièces de rechanges)…
La gestion du parc automobile est une composante de la SCM (Supply Chain Management) ou GCL (en français Gestion de la Chaîne Logistique). On appelle parc ou flotte de véhicules industriels l’ensemble des moyens de transports dont dispose une entreprise, un organisme ou un particulier qui doit effectuer de façon régulière du transport de marchandises.
Deux entreprises sont susceptibles de posséder un parc de véhicules industriels.
- l’entreprise fabriquant des biens et services qui souhaitent avoir un parc propre.
- l’entreprise de transport
Ø L’entreprise fabriquant des biens et services : Ces entreprises souhaitent avoir un parc propre parce qu’elles veulent garder la maîtrise de leurs transports en disposant des véhicules
Pour faire le transport pour compte propre il faut 3 critères :
- le véhicule doit appartenir à l’entreprise
- la marchandise doit appartenir à l’entreprise
- l’activité doit appartenir à l’entreprise
· transport public (autrui)
Contraire des critères du transport pour cpte propre.
Théoriquement, elle peut être découpée en 5 facteurs :
La marchandise influence le choix des moyens de transport et de manutention. Il est important d’avoir au préalable une information juste sur le type d’emballage ou le conditionnement des UL (Unités Logistiques) et des UM (Unités de Manutention)
(Informations qui plus tard servent à renseigner les documents de transport, permettent d’anticiper sur la nature des moyens matériels à mobiliser au lieu du chargement et au lieu du déchargement des marchandises)
Eléments clés :
Respect du dimensionnement du véhicule
Optimisation du chargement
Respect des contraintes liées aux moyens de manutention à mobiliser
Respect des conditions de transport (emballage, protection, sécurité …)
L’espace géographique influence outre le choix des moyens, mais aussi l’organisation de l’opération de transport.
Pour chaque opération de transport, il est essentiel de définir le lieu de départ, le lieu d’arrivée et les principaux points d’escales qui ensembles constituent l’itinéraire. L’organisateur de l’opération de transport peut ainsi recenser les lieux de prélèvements et de livraisons successifs des marchandises tout au long de son itinéraire et déterminer le chemin optimal.
L’itinéraire choisit permet de prévoir le nombre de barrières de contrôle, le nombre de péages routiers, les points de pesage routier et d’intégrer ces éléments dans le cahier de charge du chauffeur.
L’espace géographique enfin permet de prendre aussi en considération l’état des routes, le relief, le climat, les mœurs de populations qui influencent chacun à sa manière le choix du véhicule et le choix des horaires dans le planning. Ex. ETD (estimated time of departure) et ETA (estimated time of arrival) en fonction des heures de travail dans la région
La marchandise à transporter et l’itinéraire du transport permettent de faire un premier choix du type de véhicule de transport. Trois autres contraintes vont permettre de finaliser et de valider ce choix. Il s’agit de contraintes techniques, contraintes administratives, contraintes logistiques.
Les contraintes techniques se rapportent à :
· La pneumatique (état des roues et présence de roues de secours)
· La signalisation lumineuse
· La signalisation sonore
· La présence à bord du matériel de sécurité (triangle de sécurité, extincteurs, ARI …)
· La présence du matériel de premiers secours
Ce sont là quelques uns des éléments techniques sur lesquels on peut facilement effectuer un contrôle. Cependant, la présence de la « visite technique » valide est une preuve du bon état de marche du véhicule. C’est le document administratif qui atteste que le véhicule est apte à la circulation.
Les contraintes administratives
· Les documents du véhicule ;
· Le marquage et l’étiquetage de l’automobile ;
· Les documents du chauffeur ;
· Les documents de la marchandise.
Les contraintes logistiques :
· L’avitaillement du véhicule
Ceci sous entend aussi l’intégration d’une gestion des stocks de consommables aux responsabilités du gestionnaire du parc automobile.
Le personnel affecté à un système de gestion du parc automobile est varié. Outre les chauffeurs, il existe généralement une équipe de mécaniciens, les HTM (Hommes Tout Main) et le personnel administratif.
Il est devenu difficile de dissocier gestion logistique, optimisation et technologie. La gestion du parc automobile utilise les logiciels de type TMS ( Transport Management System) ou SGT (en français Système de Gestion du Transport)
Les principales fonctionnalités :
· Gestion des stocks de consommables et de pièces de rechange
· Gestion des ressources humaines (horaires de travail/repos)
· Gestion de la maintenance
· Planification des livraisons
· Gestion des transports (traçabilité, documents de transport)
La gestion du parc automobile est pratiquée dans les entreprises de location automobile, les entreprises industrielles et commerciales. Pour ces deux dernières, elles peuvent selon les cas disposer d’un parc intérieur ou d’un parc extérieur (matériel de transport en location).
I) Les responsabilités du gestionnaire du parc automobile
II) Le gestionnaire de parc : bon comptable et super technicien
Le gestionnaire de flotte est avant tout un homme qui sait compter, qui a de solides connaissances techniques et qui sait aussi, manager des hommes »
Homme lige de l’entreprise, il a des responsabilités financières, juridiques, fiscales et techniques. un ensemble de compétences auxquelles aucune formation ne prépare véritablement et pour lesquelles aucune filière de recrutement n’existe. en conséquence, ils proviennent de tous les horizons, reçoivent une formation très souvent empirique qui, compte tenu, notamment, des évolutions techniques, doit faire en permanence l’objet de « recyclages ».
· L’homme de tous les choix
Il convient de définir les attributions qui relèvent de la fonction. Au-delà des responsabilités et des critères de compétences que nous avons évoqués, le gestionnaire de parc doit pouvoir contrôler des postes essentiels. « Si, dans ses attributions, il n’a pas un regard global sur l’entreprise, s’il n’est que financier, s’il n’est que technicien ou ne gère que les relations humaines, ce n’est plus un gestionnaire de flotte dans l’acception du terme ».
En matière de véhicule, il est en principe, partie prenante aux décisions. Il participe aux choix du véhicule en fonction des besoins qu’il a décelé dans l’entreprise. c’est lui qui déclenche le financement et doit s’interroger sur le choix des formules (achat, location, crédit-bail) et connaître la fiscalité pour en minimiser l’incidence. Parallèlement, il doit déterminer les périodes optimales de renouvellement – en termes techniques et financiers – et les prévoir.
· Maîtrise des coûts et des charges
Les choix techniques et financiers effectués, le gestionnaire de parc doit en permanence suivre les coûts d’exploitation de l’entreprise et maîtriser les charges variables. Si, dans les PME, on se réfère souvent aux évolutions de coûts qui sont publiés par le CNR ou les indices de la CLTI qui sont considérés, en général, « comme des indicateurs », les grands groupes et les entreprises qui disposent de gestionnaires de parcs développent leurs propres modèles de calcul.
Dans certaines entreprises, comme le ramassage du fait, par exemple, on pourra raisonner en centime / litre et non pas en franc / kilomètre… Quant à l’évaluation des charges variables que le responsable du parc devra ensuite maîtriser, elles concernent aussi bien les carburants que les lubrifiants ou les pneumatiques, la maintenance avec ses choix (intégrée ou sous traité) et sa planification. Bref, autant de paramètres qui rentrent dans la grille de calcul des coûts de revient et qui varient en fonction des activités de l’entreprise.
· Tableau de bord
Cela conduit le gestionnaire de parc à dresser un tableau de bord qui lui permettra d’effectuer le suivi des véhicules, de contrôler leur utilisation, opérations dont découlera la possibilité de « dimensionner » le parc dans le temps en termes de volume et de capacité.
Il n’aura plus, alors, qu’à informatiser la gestion du parc à partir de logiciels qui sont aujourd’hui nombreux sur le marché et qui sont de plus en plus performants.
I) La gestion de parc, outil de la qualité, outil de qualité
Dans les deux cas, le parc de véhicule industriel est un élément essentiel de la qualité du transport, donc au bien à transporter. Comme toute activité, le transport doit être adapté aux besoins du client. Le parc de véhicules en constitue l’outil de performance. La qualité du taux de service dépendra de la qualité de cet outil.
La gestion de parc a donc un double objectif :
- Qualité (adapter les moyens aux besoins, mais pas à n’importe quel prix)
- Rentabilité (maitrise des coûts, augmentation de la disponibilité du parc) sont les suivantes :
· Fréquence d’utilisation des véhicules élevés
· Taux de chargement important
· Maintien des taux transportés dans une chaine intégrée ‘’Production, commercialisation, distribution’’.
- Parce qu’elles sont soumises à des contraintes d’ordre :
· Techniques (fragilité ou confidentialité des taux, mis en place par des spécialistes, maison, délais de livraison).
· Commerciales (contacts directs avec des fournisseurs et des clients, facturation sur place, encaissement, prise de commandes).
· Promotionnelles
II) LA GESTION DE PARC, ACTIVITE MULTIPLE
A) Les Eléments de la gestion de parc
La gestion de parc est un ensemble d’opération diverses telles que :
- Définir une politique d’acquisition et de vente
- Mettre à jour des connaissances, poursuivre l’évolution technique des matériels
- Rechercher des sources de financement spécifiques compte tenu de la nature particulière des actifs
- Intégrer dans l’entreprise un atelier d’entretien et de réparation spécialisée ou rechercher des spécialistes extérieurs avec qui on passe des accords précis et dont on surveille l’exécution.
- Acheter aux meilleurs conditions le carburant et contrôler avec précision la …
- Souscrire les assurances nécessaires pour assurer le suivi de l’exécution du CT et du règlement des sinistres
- Recruter, former, encadrer un personnel distinct de celui qui concourt à l’activité principale de l’entreprise.
- Mettre en place un système d’information et comptable
B) Le classement des opérations de gestion de parc
La gestion technique
- Organisation de la maintenance
- Suivi des consommations
- Exploitation du parc
- Gestion de stock
Véhicules :
C.U = 0,60 x 0,65 = moyenne
C.U < 0,60 sous exploités
C.U > 0,65 exploitation efficiente rationalité.
Si le C.U est de 0,90, ils sont surexploités.
La gestion financière
ü suivi des coûts de revient
ü suivi des coûts kilométriques
ü suivi des coûts périodiques
ü suivi des coûts de structures (frais de gestion, coûts indirects)
ü renouvellement des véhicules
ü choix de la formule d’acquisition et de financement (leasing…)
Gestion du personnel
ü suivi de l’activité du personnel
ü Gestion du personnel
o Sélection du personnel
o formation du personnel (formation de base, formation spécifique)
A. ORGANISATION ET PLANIFICATION DE LA MAINTENANCE
2) La maintenance
La maintenance
industrielle ou générale est devenue depuis une dizaine d’années une discipline
à part entière avec ses concepts, ses méthodes, ses enseignements et, consécration
moderne, ses progiciels informatiques. En un chapitre, il ne peut être question
d’épuiser un tel sujet qui n’appartient d’ailleurs pas en tant que tel au
domaine logistique. On surprendrait la plupart des ingénieurs ou techniciens de
maintenance par un tel rattachement sauf en ce qui concerne les activités de
service après vente. En effet, si la planification des activités de maintenance
d’un système complexe appartient d’évidence à la logistique à travers le SLI,
les activités de maintenance proprement dites sont des activités techniques au
même titre que la production ou l’ingénierie.
On n’abordera donc ici, et encore sommairement, que les principes et méthodes
utiles à la planification de la maintenance lors de la conception d’un système.
En ce qui concerne les définitions, deux normes françaises Afnor 60-010 et
60-011 définissent, avec plus ou moins de bonheur, certains termes de base de
la maintenance.
1-1)Les différents types de maintenance
La norme Afnor X 60-015 distingue différents types de maintenance selon le schéma suivant :
La
« maintenance » est définie comme « l’ensemble des
actions permettant de maintenir ou de rétablir un bien dans un état spécifié ou
en mesure d’assurer un service déterminé ».
La « maintenance corrective » est la
maintenance effectuée après défaillance.
Cette appellation n’est pas très heureuse car l’usage anglo-saxon est d’appeler
corrective maintenance une maintenance apportant des améliorations
augmentant par exemple la fiabilité ou la maintenabilité d’un bien. Dans
l’industrie, on parle le plus souvent de maintenance
« curative » pour désigner ces interventions après panne.
La « maintenance préventive » est la
maintenance effectuée dans l’intention
de réduire la probabilité de défaillance d’un bien ou d’un service rendu.
La « maintenance préventive systématique
» est « une maintenance effectuée
selon un échéancier établi selon le temps ou le nombre d’unités d’usage. » On
distingue le plus souvent dans l’industrie la « maintenance programmée », que
l’on peut prévoir à l’avance et constituée de maintenances préventives,
révisions, remises à niveau ou réparations différées, et la maintenance non
programmée qui correspond à la suppression des dysfonctionnements (pannes,
défauts de qualité, insuffisance de rendement, etc.).
La « maintenance préventive
conditionnelle » est « une maintenance subordonnée à un type d’événement
prédéterminé (mesure, diagnostic). »
La « réparation » est « une
intervention définitive et limitée de maintenance
corrective après défaillance. »
Le « dépannage » est « une action
sur un bien en vue de le remettre provisoirement en état de fonctionnement
avant réparation. » En pratique, on parle de « dépannage » sans effectuer le
plus souvent cette distinction entre « réparation » et « dépannage ».
3) Les opérations constitutives de la maintenance
La disponibilité
Toute maintenance à pour objectif d’obtenir une sécurité suffisante pour que le matériel assure un service suffisant pendant un certain nombre de milliers de km. Ou d’heures de fonctionnement, cet aptitude est souvent appelée disponibilité. La disponibilité du véhicule dépendra de la disponibilité de chacun de ses composants. Le véhicule industriel est composé d’un certain nombre d’organe : moteur, boite, pompe, direction, carrosserie, équipement et divers sous-composants. Chacun de ces éléments a sa durée de vie ou son espérance de vie propre. Elle dépend en toute autre les conditions d’exploitation du matériel. Les interventions devront donc être faite des intervalles plus en qui notamment :
- Les conditions d’exploitation du matériel (livraison urbain, chantier)
- Le large du matériel (intervalle entre 2 interventions sous le même composant à tendance à diminuer avec le vieillissement.
Le ravitaillement
Le ravitaillement consiste non seulement à faire le plein de carburant mais à parfaire le niveau d’huile (le moteur diesel peut briller jusqu’à 1% de son huile) les niveaux d’eau du radiateur, de batterie, des circuits annexes. Les éventuels équipements auxiliaires tels qu’un groupe de réfrigérateur, le malaxeur à béton.
L’entretien
Ce sont des opérations à caractère permanent qui s’effectuent systématiquement tout au long de la durée de vie du véhicule. Elles peuvent être périodiques. EX : Tous les 5 000 ou 10 000 km ou saisonnières. Elle est uniquement applicable dans le cas d’un parc rigoureusement homogène (40T unique). Il s’agit donc de dénombrer sur un exo la quantité de pneus neufs, rechapage et retaillage consommés. En déduire un être actualisé à la date de cette étude et diviser ce tonnage Par le km parcouru par les véhicules du parc.
Comme tout matériel, le parc de véhicule doit être maintenu en tout état de marche.
La politique de maintenance
Différenciation des pneumatiques
On différencie selon l’emplacement du pneumatique sur le véhicule :
- La semi remorque ou le tracteur ou porteur la semi
- Essuie moteur ou directeur
On tient également compte de l’utilisation qui sera faite du véhicule.
-Suivi des pneumatiques
Il pourra être opéré au niveau administratif avec la fiche pneumatique et en ce qui concerne les coûts De revient.
Le coût
Le coût d’un pneumatique est propre au kilométrage parcouru. On tâchera d’évaluer le coût du pneumatique et de le rapporter en nombre de km effectué. On dispose de trois méthodes :
- Méthode d’abonnement (1)
- Méthode globale (2)
- Méthode générale (3)
(1) : Elle consiste à souscrire un coût avec le fournisseur de pneus. Ce dernier facturera le km parcouru en contre partie, il assurera la facture et la surveillance des pneus.
Structure du pneumatique :
- La ceinture
- La carcasse
- La flâne
- Le talon
- Le renfort talon
La bande de roulement assure la résistance de l’usure toute en garantissant une assistance adhérente maximale avec le sol avant ou après le retaillage.
La ceinture stabilise la bande de roulement et garantit une circonférence de roulement.
La carcasse transmet toutes les forces traction de freins et de freinage. Elle contient la pression d’air, la couche de gomme extérieure empêche la pénétration de l’air dans la carcasse.
La flâne protège la carcasse contre les frottements, les blessures et le phénomène d’ozonisation.
Le renfort talon protège le talon contre l’abrasion sur les rebords de gente.
Le talon permet la fixation de la carcasse sur la gente et assure avec l’élément carcasse les forces directionnelles aux éléments ceinture et bande de roulement pour une bonne tenue de trajectoire.
Détermination des coûts d’exploitation et rentabilité en transport
Le temps total nécessaire à la réalisation d’une tournée correspond aux opérations de :
- Manutention et chargement du véhicule au dépôt
- Transport d’approche jusqu’au premier client
- Déchargement chez le client (n fois)
- Parcours jusqu’au client suivant (n fois)
- Retour au dépôt
La connaissance de la durée de la tournée et du kilométrage réaliser permet de calculer aisément le coût de celle-ci. En effet, le coût d’exploitation du véhicule s’exprime habituelle sous la forme suivante :
Coût d’exploitation = frais fixes + frais variables/Km
Application 1
La société Armand S.A voudrait réviser sa politique de gestion. Elle dispose d’un parc automobile de véhicule de 10 tonnes de charge utile ayant les informations suivantes :
26 200 000FCFA/an + 163,75FCFA/km. Son organisation logistique actuelle repose sur la réalisation de deux circuits de desserte par jour et par camion de 150 Km chacun sur une période annuelle de 240 jours.
TAF :
1) Expliciter l’expression : 26200000FCFA/an + 163,75FCFA/Km.
2) Calculer le coût d’exploitation annuelle, puis d’une tournée.
3) En considérant la demande en annexe comme étant fixe le long de l’année, déterminer les coûts d’exploitation annuelle, hebdomadaire et moyenne.
4) Si la tarification appliquée au client est de 25F/tonne/Km, l’entreprise va-t-elle générer des bénéfices ?
Annexe
Lundi |
Mardi |
Mercredi |
Jeudi |
Vendredi |
17t |
19t |
8t |
20t |
9t |
Application 2 : rentabilité d’une activité de transport
Vous êtes chargé d’étudier la rentabilité d’une proposition de trafic faite par un chargeur. Cette proposition concerne un lot complet, occupant un véhicule de 40 PTRA de l’entreprise.
Transport de marchandise de Yaoundé-Bafoussam (340 Km/aller) faisant l’objet d’un contrat l’année, à raison de 4 départs et retour par semaine. L’entreprise fonctionne 46 semaines par an, l’exploitation du véhicule se fait sur 203 jours.
Les charges fixes annuelles s’élèvent à 110 229 XAF, le prix de vente unitaire : 1,5F/Km
1) Quelle est la différence entre un véhicule porteur et un tracteur
2) Que signifie PTAC, charge utile, PTRA, poids mort ?
3) Calculer le chiffre d’affaires annuel de cette entreprise.
Les charges variables au Km sont données par :
- Consommation carburant 33 litre/100 Km à 1 XAF par litre.
- Entretien et réparation : 0,04 XAF/Km
- Péage : 0,20 XAF/Km
- Pneumatique : on utilise ½ train de pneus par an
Tracteur : 6 pneus à 650 XAF l’un ; semi-remorque : 6 pneus à 700 XAF l’un
4) Calculer les charges variables totales annuelles et déduire la marge sur coût variable
5) Calculer le seuil de rentabilité en valeur et en quantité
6) Déterminez la date à laquelle le seuil de rentabilité sera atteint.
Application 4
Le responsable logistique de la société Arro vous demande d’étudier la rentabilité d’une proposition de trafic faite par un chargeur (nommé TEX) lors d’un entretien effectué entre les directeurs des deux sociétés.
Cette proposition concerne un lot complet occupant un véhicule de 40 tonnes de l’entreprise.
TAF : A partir des éléments contenus en annexe, déterminer :
1) Les charges variables totale annuelle, journalier et par kilomètre de l’entreprise
2) Les charges fixes totales du véhicule et du conducteur par an et par jour
3) Les charges de structure par jour
4) Le chiffre d’affaire annuel de l’entreprise
5) Le chiffre d’affaire critique en valeur et en quantité
6) La date à partir de laquelle le seuil de rentabilité est atteint
NB : les calculs se feront dans des tableaux
Annexe
Proposition du trafic
- Transport d’un lot complet de Sousse-Tunis (340 Km) faisant l’objet d’un contrat à l’année, à raison de 4 départs et retours par semaine.
- L’entreprise fonctionne 46 semaines par an, l’exploitation du véhicule se fait sur 203 jours.
- Le prix proposé par le chargeur est de 1,500 FCFA/Km.
Eléments de calcul du coût du véhicule 40 tonnes
- Consommation carburant : 33 litres/100 Km à 1 FCFA/litre
- Acheté le 01/01/2006 à 100 000 FCFA HT (remorque + véhicule)
- Entretien et réparation : 0,040 FCFA/Km
- Péage : 0,200 FCFA/Km
- Pneumatiques : compter ½ train de pneus par année
- Tracteur 6 pneus à 650 FCFA L’un
- Semi : 6 pneus à 700 FCFA l’un
- Salaire conducteur : 800 FCFA brut/mois + 13ème mois
- Charges sociales : 48% du salaire brut
- Frais de route : 20 FCFA/Jour
- Taxe sur véhicule : 650 FCFA/an
- Financement du véhicule : 2 800 FCFA/an
- Amortissement dégressif sur 5 ans
- Assurances : 8000 FCFA/an
- Charges de structures annuelles : 25 000 FCFA (ce montant correspond uniquement au véhicule utilisé par ce transport).
Application 5
La plateforme logistique de l’entreprise ARRO vient d’acquérir un ensemble d’outil composé d’un tracteur et d’une semi-remorque pouvant transporter 30 palettes. Le tracteur a été acheté à 75 000 euro (amortissable linéairement sur 5 ans) et la semi-remorque à 25 000 euro (amortissable en 7 ans). Le tracteur consomme environ 35 litres de gasoil au 100 Km (à 0,9 euro/litre) il fonctionne 220 jours/ans et est affecté au livraison de proximité (magasin situé à moins de 50 Km de la plateforme, soit dans la zone une) il effectue 3 tournées par jour soit environ 225 Km/jour. Le poste entretien, réparation et pneumatique représente un coût variable de 0,14 euro/Km. L’assurance et la taxe à l’essieu qui sont des coûts fixe se montent respectivement de 4 000 euro et 8 000 euro/an. On admettra pour les différentes questions un taux de remplissage de 30%. En votre qualité de consultant manageur, vous répondrez aux questions suivantes :
1) Donnez un distinguo entre la logistique de « faire et de faire, faire »
2) Quelles sont les composantes de la logistique de « faire, faire »
3) En retenant un salaire hors charge de 1200 euro/mois (sur 12 mois) pour le chauffeur, un coefficient de charge sociale de 50% et des frais financiers annuels de 3 740 euro
Déterminer le coût journalier de fonctionnement de ses véhicules
4) M. ARMAND vous propose un véhicule comparable un tarif de 90 euro au tour, sur la base de 3 tours /jour. Que pensez-vous ? de cette offre ?
5) Il peut également utiliser un porteur d’une capacité inférieur (20 palettes) au prix de 67 euro le tour, toujours sur la base de 3 tours/jour. Cette nouvelle proposition représente-t-elle de l’intérêt ? Si oui, dans quel cas ?
6) Quels avantages et inconvénients présentent la sous-traitance du transport ?
7) Comparer les coûts de livraisons d’une palette de PGC (produits de grande consommation), contenant 1000 euro de produits, à une surface de vente située dans la zone 1 (3 tournées par jour), dans la zone 2 (ou compte tenu de la distance, un véhicule ne peut faire que 2 tournées par jour et dans la zone 3 seulement une tourné par jour. On retiendra le tarif proposé par M. ARMAND dans la question 4. Exprimer votre résultat en pourcentage de la valeur de la palette.
CHAPITRE 3 : GESTION DES RESSOURCES DE PRODUCTION : CHARGE/CAPACITE
Lorsque les lancements de production sont déterminés, on peut calculer les charges résultantes pour les différents ateliers. Pour que ce plan de production soit réaliste, il faut que la charge résultante respecte les capacités de production. Si c’est n’est pas le cas, un ajustement charge/capacité est effectué.
I) Capacité d’une ressource
1) Définition
La capacité d’une ressource est quantité de produit obtenu dans les
conditions normales d’exploitation. En d’autres termes, c’est la quantité de
flux de matière que cette ressource peut traiter par unité de temps. On peut
dire que l’aptitude d’une ressource à traiter les flux. Elle peut être mesurée
par un temps de
fonctionnement par rapport à un intervalle de temps donné, Exemple : 8h par
jour ou par un débit de production par rapport à un intervalle de temps donné, Exemple :
50 pièces par heure.
Les ressources de production : sont l’ensemble des moyens
permettant de transformer les matières premières en produits finis ou semi-finis. On distingue :
· Les ressources humaines
· Les ressources matérielles
· Les ressources financières
· Les ressources informationnelles et
technologiques
Les ressources sont évaluées à partir de leur capacité.
Lorsqu’un atelier est constitué de plusieurs ressources, sa
capacité dépend du type de montage.
a) Montage en série
Lorsque le montage est en série, la capacité de l’usine est celle
de la ressource goulet (la machine ayant la plus petite capacité).
b)
Montage en parallèle
Dans le cadre d’un montage en parallèle, la capacité de l’atelier
est la somme des capacités des machines.
Application
1
L’atelier d’une usine est constitué de 3 machines A1, A2, A3 dont les capacités
respectives de
traitement sont 20 pièces par heure, 15 pièces par heure et 30
pièces par heure.
TAF : déterminer la capacité horaire de cet atelier dans les cas
suivants :
a- Le montage est en série
b- Le montage est en parallèle
Application 2
L’atelier d’une usine est constitué de 4 machines (M1, M2, M3 et M4) dont les capacités respectives sont 30 pièces/h, 25 pièces/h, 40 pièces/h et 50 pièces/h.
Travail à faire : déterminer la capacité horaire de cet atelier dans les cas suivant :
- Le montage est en série
- Le montage en parallèle
2) Notion de capacité théorique et capacité effective
On distingue la capacité théorique et la capacité effective
a) La capacité théorique : c’est la capacité d’une ressource hors système de production. Pour les machines et les équipements, elle est donnée par le constructeur
b) La capacité effective : c’est la capacité d’une ressource implantée dans un système de production.
La différence entre la capacité
théorique et la capacité effective
est la chute ou la perte de
capacité. Elle est causée par :
*Les arrêts de
production dû aux changements d’outils
*Les pannes des machines
*Les réglages
*Les nettoyages
*Les rebus
*Les absentéismes
* les incident technique (panne diverses).
Application
3
Une usine de la place dispose de 3 postes P1, P2, P3 montés en
ligne dont les capacités horaires sont respectivement 20 pièces, 30 pièces et 25 pièces. Le temps de
travail est 8h par jour et il y a 20 jours ouvrables par mois. Le poste P2 a un taux de rebus de 5% et le
temps de réglage coûte 1h au poste P3.
TAF :
1) Déterminer les capacités mensuelles théoriques en nombre de
pièces de chaque poste
2) Déterminer les capacités effectives des postes
3) Comment appelle- t- on la différence entre la capacité
théorique et la capacité effective, qu’est ce qui est à l’origine de cette
différence dans ce cas ?
Application 4
Dans une industrie manufacturière, le règlement prévoit 8 heures de travail par jour pendant 25 jours ouvrables par mois. Une machine installée dans cette usine traite 200 pièces par heure. Cette machine nécessite un réglage de 1,5 h/jour avec un taux de rebus de 4%.
a) Déterminer la capacité théorique de cette machine.
b) Déterminer la capacité théorique mensuelle en nombre d’heure et nombre de pièce pour cette machine.
c) Déterminer la capacité mensuelle effective en nombre d’heure et en nombre de pièce
d) Comparer les résultats et commentés.
II) La charge
La charge : la charge travail est la demande de la clientèle
traduite soit en nombre d’heures de
travail à effectuer ; soit en nombre de pièces à fabriquer. En
d’autre terme c’est la quantité de flux qu’une ressource doit délivrer. Tout
comme la capacité, on distingue la charge théorique et la charge effective.
Application
5
Considérons l’application 3 précédent et que cette entreprise reçoit une
commande mensuelle de 4 000 pièces.
TAF :
1) Combien de pièces faut-il lancer pour satisfaire la demande
2) Déterminer les charges en nombres de pièces et en nombres
d’heures de chaque poste.
Application 6
Une usine fonctionne 8 heures par jour pendant 20 jours ouvrabales par mois. Elle a installée qui traite 100 pièce/h. cette machine nécessite un réglage quotidien d’une heure et le taux de rebus est de 2%. L’usine a reçu une demande de 15000 pièce/ mois.
Travail à faire :
1) Déterminer la charge théorique mensuelle en pièce et en nombre d’heure.
2) Déterminer la charge effective mensuelle en nombre de pièce et en nombre d’heure.
3) Comparer les résultats et commenter.
III) Notion de ressource goulet
On appelle ressource goulet, une ressource dont la capacité ne permet pas de satisfaire la demande. C’est une ressource qui limite la capacité des autres ressources. En bref c’est la ressource qui a la plus petite capacité dans un une gamme de fabrication. Une gamme de fabrication est la succession d’action pour réaliser un produit donné.
Application
Considérons l’exercice précédent (application 6). Dans lequel des cas suivant la machine est une ressource goulet ?
- Une demande de 10 000 pièces/mois
- Une demande de 20 000 pièces/mois.
IV) Déséquilibre charge/capacité
Les ressources dont dispose l’entreprise ne sont pas toujours en adéquation avec la demande sur le marché. Il peut exister un déséquilibre entre les deux. Il y a déséquilibre entre charge et capacité dans les cas suivant :
- Lorsque la charge est supérieure à la capacité : on dit que l’entreprise est en suractivité.
- Lorsque la charge est inférieure à la capacité : on dit que l’entreprise est en sous activité.
V)
Recherche de l’équilibre charge/capacité
Ø Lorsque la charge est supérieure à la capacité : dans cette
situation
(suractivité), les actions suivantes peuvent permettre de
rétablir :
§ Produire par stock anticipé ;
§ Acheter de nouvelles machines ;
*Embaucher les temporaires ;
§ Faire recours à la sous-traitance ;
§ Augmenter les heures de travail ;
§ Développer une polyvalence des ressources (c’est l’aptitude d’une
ressource à traiter les flux de nature différentes).
Dans le cas
d’une entreprise de service :
§ Faire participer le client au service ;
§ Développer les self-services ;
§ Accroître les agences ;
§ Segmenter la clientèle ;
§ Instaurer les services sur rendez-vous.
Ø Lorsque la charge est
inférieure à la capacité
§ Réduire les heures de travail ;
§ Chômage technique ;
§ Négocier les périodes de congé ;
§ Mettre sur pieds des tarifs promotionnels pour attirer les clients
(entreprise de services).
QUELQUES DEFINITIONS
Polyvalence
d’une ressource : c’est son aptitude à traiter les flux de nature différente.
Flexibilité
d’une ressource : c’est son aptitude à augmenter ou à réduire sa capacité.
Ressource
goulet : c’est une ressource qui limite la capacité des autres ressources
dans une gamme de fabrication ou encore c’est la ressource qui a la plus petite
capacité.
Gamme de
fabrication : suite d’opération à réaliser permettant de transformer les
matières premières en produits finis.
Application
4 postes de travail sont utilisés dans la fabrication d’un produit fini suivant la gamme P1, P2, P3 et P4 de capacité respective en nombre de pièce par jour : 310, 300, 280 et 300
TAF :
1) Déterminer la capacité effective mensuelle en nombre d’heure et en nombre de pièce pour chaque poste de travail et pour la chaine de travail.
2) La demande reçue par l’entreprise est de 6500 unités. Dite si elle sera satisfaite. Si non quelles mesures correctives peuvent être prises.
3) Pour cette demande, calculer la charge effective mensuelle en nombre d’heure et en nombre de pièce pour chaque poste
Information complémentaire :
Un mois à 20 jours ouvrables, une journée à 8 heures de travail. Le poste P2 a un taux de rebus de 3%. Le poste P3 nécessite 1 heure de réglage au quotidien.
CHAPITRE 4 : LE PILOTAGE ET LE DIAGNOSTIC LOGISTIQUE
INTRODUCTION
Le diagnostic est un examen qui consiste à identifier les causes d’un mauvais fonctionnement, à établir un pronostic et à proposer des solutions. Le diagnostic Logistique est un « examen critique » des points forts et des points faibles du système logistique de l’entreprise. Il conduit nécessairement à déterminer un plan d’actions, ces actions sont elles-mêmes évaluées en coût de mise en œuvre et de gains quantitatifs et qualitatifs.
Il vise souvent à permettre la réalisation d’un projet de dimension en s’appuyant sur la mobilisation des facteurs internes de l’entreprise.
Les approches en matière de diagnostic sont par rapport à un périmètre donné de rechercher et de détecter les éventuelles défaillances et disfonctionnement des process. A l’issue d’un diagnostic, le PDG de l’entreprise a à sa disposition l’ensemble des éléments lui permettant de prendre des décisions.
I) OBJECTIFS DU DIAGNOSTIQUE
· Observer pour comprendre
Il s’agit de faire un état des lieux détaillé, de bien comprendre les pratiques existantes relatives au processus en terme de fonctionnement interne et de coordination avec les autres entités de la chaînes logistique.
· Analyser pour identifier
Il s’agit de déterminer les axes prioritaires de travail et les efforts à consacrer en termes de redéfinition des processus d’une part, et d’intégration de ces processus dans ‘organisation d’autres part.
· Evaluer pour proposer
Il s’agit de rechercher et/ou concevoir, pour chaque axes de progrès les solutions possibles et d’évaluer leur pertinence.
I) TYPOLOGIE DES OUTILS
La démarche de la qualité propose toute une panoplie d’outils d’aide (méthode, analyse, statistique, suivi du contrôle). Ces outils, crées et/ou diffusés par les principaux fondateurs de la démarche qualité dans le cadre de leurs actions de conseil auprès des entreprise, ont vocation pédagogique. Il est utile de repartir les outils de la qualité en deux catégories :
Ø Les outils complexes utilisés
dans les domaines de l'ingénierie, de la logistique, de la
métrologie, des statistiques, par les services de planification et de méthode.
Ø Les outils simples d'aide
à la réflexion, à l'analyse, à la méthode, utilisables par tout public
sans formation particulière (1-Diagramme de Pareto, 2-diagramme causes-effets,
3 stratification, 4-check-list, 5-histogramme, 6-diagramme de dispersion,
7-graphe / carte de contrôle).
Les différents types d’outils de pilotage sont :
a) Pour cadrer le pilotage
· Il est possible d'utiliser la roue de Deming :
La méthode PDCA est une démarche cyclique d’amélioration qui consiste, à la fin de chaque cycle, à remettre en question toutes les actions précédemment menées afin de les améliorer. PDCA tire son origine des premières lettres des mots qui la composent : Plan-Do-Check-Act. Ces derniers peuvent être interprétés tel qu’il suit :
- Plan : Préparer, Planifier ;
- Do : Développer, réaliser, mettre en œuvre ;
- Check : Contrôler, vérifier ;
- Act (ou Adjust): Agir, ajuster, réagir.
Cette méthode a été rendue populaire suite à sa présentation au Nippon Keidanren dans les années 50 par le célèbre statisticien William Edwards Deming. Deming illustre le principe PDCA par une roue qui sera ensuite baptisée : La roue de Deming.
La roue de Deming est un cercle vertueux divisé en quatre portions et présenté sur la diagonale d’un triangle. Sur chacune des portions, est marquée une lettre P-D-C-A dans le sens des aiguilles d’une montre. Lorsqu’on tourne la roue dans le même sens, elle grippe sur la diagonale en passant sur chaque étape jusqu’à la fin du cycle. Ensuite, on recommence avec le cycle suivant. L'idée est de répéter les 4 phases : Plan - Do - Check - Act tant que le niveau attendu n'est pas atteint.
- La première étape du cycle :
(Plan) en français « Planifier », consiste à préparer et planifier ce que l’on va réaliser. Définir le cahier des charges (taches à réaliser et leur coût), établir un planning (déterminer les dates de début et fin de réalisation). Objectif est d’identifier le vrai problème, rechercher les causes racines et planifier la mise en œuvre des actions correctives.
- La seconde étape du cycle
(Do) en français « faire » est la construction, la réalisation, de l'œuvre. L’objectif est d’exécuter le plan d’action, déployer les ressources nécessaires et mettre en œuvre toutes les opérations correctives mentionnées dans le plan.
- La troisième étape du cycle
(Check) en français « vérifier » consiste à contrôler que les ressources mises en œuvre dans l’étape précédente (Do) et les résultats obtenus correspondent bien à ce qui a été prévu (Plan). Divers moyens de contrôle sont alors déployés (Tableau de bord : indicateurs de performance…). L’objectif est de Contrôler que les ressources mises en œuvre dans l’étape précédente (Do) et les résultats obtenus correspondent bien à ce qui a été prévu (Plan)
- Enfin la dernière étape du cycle
(Act) en français « agir », consiste à ajuster les écarts, rechercher des points d'améliorations. Ce qui amènera un nouveau projet à réaliser, donc une nouvelle planification à établir. Et ce sera le début d’un nouveau cycle. L’objectif est d’Ajuster les écarts, vérifier que les solutions mises en place sont efficaces dans le temps, rechercher des points d'améliorations tant que le niveau attendu n'est pas atteint
Selon l’illustration de Deming, on représente une cale sous la roue pour éviter de revenir en arrière. Cette dernière symbolise l’entretien d’un système formel avec des procédures claires, écrites et accessibles, des audits réguliers…
b) Pour analyser un fonctionnement
· L'outil PERT (Project Evaluation and Review Technique, litt. "technique d'évaluation et d'examen de projets"), méthode de gestion de projet permettant de définir les tâches et délais d’un projet et d’en assurer le suivi.
c) Pour rechercher les causes des défauts et qualifier leur impact
· Le Diagramme de causes et effets ou diagramme d'Ishikawa Kaoru Ishikawa (synonyme : diagramme en arêtes de poisson). Diagramme permettant d'examiner les causes profondes des problèmes. En posant continuellement la question « Pourquoi ? », on finit par découvrir la véritable cause du problème. Généralement utilisé pour mettre en évidence les causes d'un problème et les regrouper dans des catégories distinctes (par. ex. méthode, main-d'œuvre, matériel, milieu, matières).
Le professeur ISHIKAWA dans ses travaux de recherche pour améliorer la gestion de la qualité à proposer un diagramme pour analyser les causes d’un dysfonctionnement : c’est le diagramme causes-effets ou ISHIKAWA ou 5M. Il s’agit de procéder à un inventaire qu’on appelle audit des causes de dysfonctionnement dans l’entreprise, cet audit qui peut être interne ou externe permet d’identifier les causes possibles d’un effet constaté afin de déterminer des moyens pour y remédier. Le diagramme d’ISHIKAWA se présente sous la forme d’arêtes de poisson classées en catégories de causes inventoriées selon la loi des 5M (Méthode, Matière, Matériel, Milieu, Main d’œuvre). Il est constitué :
- D’une arête centrale sous la forme de flèche horizontale tracée de la gauche vers la droite et qui représente le problème à analyser au bout de la flèche dans un cadre,
- Cinq arêtes obliques partant du haut et du bas et aboutissant à l’arête centrale.
Elles représentent les cinq éléments clés d’une chaîne de qualité dans l’entreprise notamment :
· Le milieu (M1) : concerne les causes liées à l’environnement de travail (la situation géographique, les effets sonores, la luminosité)
· La Méthode (M3) : concerne les causes liées aux procédures ou mode opératoire utilisé,
Planning, la façon de faire.
· Le matériel (M4) : concerne les causes relatives aux machines, équipements et les
MoyeCe cours nous permettra de faire une initiation de nos étudiant au concepts de base du Management et de la stratégie dans les entreprises. Et surtout d’aller au-delà des aspects « scientifiques » portant sur la connaissance des notions de base du management et de l’histoire de son développement. Le but principal ici étant de montrer toute l’importance du management stratégique pour la gestion des organisations en général et les entreprises en particulier. Ceci passe par:
Définition des organisations. Définition du management. Notion d’entreprise. Fonctions du processus de management: planification, organisation, direction et contrôle. Approches théoriques du management des organisations